Characteristics and Molding Differences between Traditional (straight) Screws and V-shaped Screws
Injection molding is an important process in the production of electrical connectors, where the plastic housings of the connectors are typically made during the injection molding stage. This involves injecting melted plastic into metal molds, which then rapidly cool and solidify. The screw is a critical component of the injection molding machine, used for conveying, compacting, melting, mixing, and applying pressure to the plastic. Below, based on Greenconn's years of experience in connector production, engineers have summarized the characteristics and molding differences between two different types of injection molding machine screws (traditional straight screws and V-shaped screws).
Straight Screw Method: In the case of the straight screw method, the difference between the downward force of resin extrusion screw and the controlled back pressure determines the density of the metered resin. The density of the resin changes depending on the magnitude of the back pressure.
Figure 1: Characteristics of Traditional (Straight) Screws
Electric Hydraulic Hybrid V-shaped Method: The V-shaped method contains a back-flow prevention mechanism, which has more advantages over the straight screw method's non-return ring.
Figure 2: Characteristics of V-shaped Screws
The following compares the molding differences between V-shaped screws and straight screws in three aspects:
1.Stability of Actual Filling Amount in the Filling Process
Straight Screw Method: The straight screw has a non-return ring, which cannot control the resin cutoff amount at the beginning of the molding process, leading to unstable filling amounts in the position command control, necessitating supplementary filling through the holding pressure process.
V-shaped Screw Method: Because the V-shaped screw does not have a non-return ring, a certain filling amount can be ensured at the beginning of the molding process, reducing the occurrence of insufficient plastic molding due to premature solidification of the gate during the holding pressure stage.
Figure 3: Comparison of two filling methods
2. Stability of Resin Melting State
Straight Screw Method: The material supply position can move, causing changes in resin temperature.
V-shaped Screw Method: With the screw rotating in a fixed state, the resin supplied from the plastic inlet can undergo a certain heating process, ensuring a stable melting state.
Figure 4: Comparison of the melting state of resin in two methods
3. Setting of Back Pressure
V-shaped Screw: The metering method using a plunger does not require a plastic inlet, allowing a certain back pressure unaffected by this change to be provided to the resin being metered, resulting in very stable and effective resin density measurement.
Figure 5: Comparison of back pressure settings in two methods
Characteristics of V-shaped Injection Molding Machine:
Straight Screw Method: In the case of the straight screw method, the difference between the downward force of resin extrusion screw and the controlled back pressure determines the density of the metered resin. The density of the resin changes depending on the magnitude of the back pressure.

Electric Hydraulic Hybrid V-shaped Method: The V-shaped method contains a back-flow prevention mechanism, which has more advantages over the straight screw method's non-return ring.

The following compares the molding differences between V-shaped screws and straight screws in three aspects:
1.Stability of Actual Filling Amount in the Filling Process
Straight Screw Method: The straight screw has a non-return ring, which cannot control the resin cutoff amount at the beginning of the molding process, leading to unstable filling amounts in the position command control, necessitating supplementary filling through the holding pressure process.
V-shaped Screw Method: Because the V-shaped screw does not have a non-return ring, a certain filling amount can be ensured at the beginning of the molding process, reducing the occurrence of insufficient plastic molding due to premature solidification of the gate during the holding pressure stage.

2. Stability of Resin Melting State
Straight Screw Method: The material supply position can move, causing changes in resin temperature.
V-shaped Screw Method: With the screw rotating in a fixed state, the resin supplied from the plastic inlet can undergo a certain heating process, ensuring a stable melting state.

3. Setting of Back Pressure
V-shaped Screw: The metering method using a plunger does not require a plastic inlet, allowing a certain back pressure unaffected by this change to be provided to the resin being metered, resulting in very stable and effective resin density measurement.

Characteristics of V-shaped Injection Molding Machine:
- Melting at a certain temperature, metering at a certain density: By rotating the screw at a certain position, the meltable resin will push the plunger up to the metering point. The position for metering will be memorized on the controller, ensuring a fixed resin density during metering.
- Filling at a certain time, with a certain amount: With an encoder resolution of 0.5µm accuracy and closed-loop speed control, the filling time from the metering position to the V-P position remains fixed even if there are changes in resin viscosity or temperature. With the plunger, there is no back-flow, enabling quantified filling.
- Maintaining a certain time and pressure during holding: Pressure sensing with a pressure sensor of precision MAX pressure/4000 in 0.0-second units can achieve closure during holding. Furthermore, because of the plunger and hydraulic control, effective holding can be performed under good pressure.
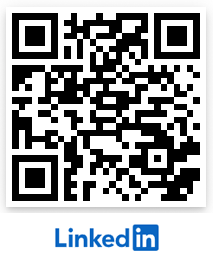
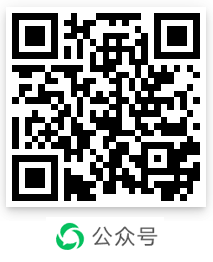